Factory Electrical Maintenance: Comprehensive UK Guide
Ensure safety and efficiency in your factory with our detailed maintenance guide. Learn about inspections, testing, and services from Birmingham’s TLO Electrical Services.
MANUFACTURING
Martin Pegg
5/8/20242 min read
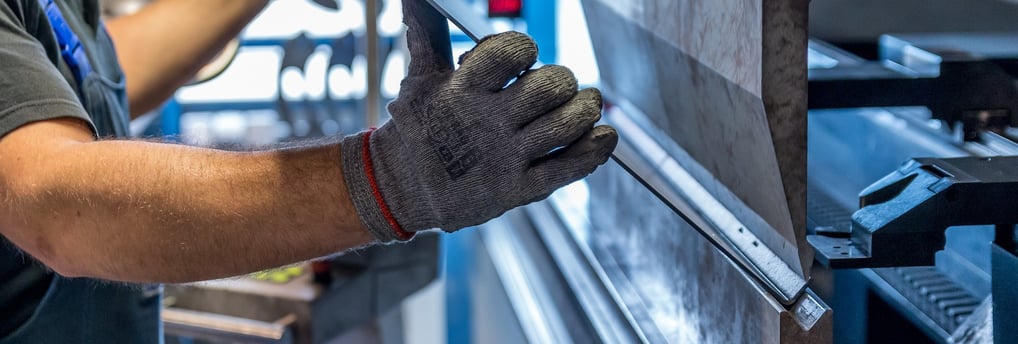
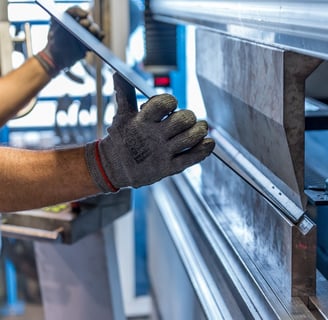
Comprehensive Guide to Factory Electrical Maintenance
Maintaining a safe and efficient factory environment relies heavily on proper electrical maintenance. This process ensures smooth operations, reduces safety risks, and prevents costly downtime. For businesses in Birmingham and the West Midlands, TLO Electrical Services (www.tloelectrical.co.uk) provides expert electrical maintenance solutions tailored to industrial needs.
Why Electrical Maintenance is Crucial for Factories
Factories operate with high-energy consumption, powering machinery essential for production. Without routine maintenance, electrical systems are prone to wear and tear, which can lead to:
Safety Risks: Faulty wiring or overloaded circuits increase the risk of electrical fires or shocks.
Operational Delays: Sudden electrical failures disrupt productivity.
Regulatory Non-Compliance: Factories must adhere to UK standards, including the Electricity at Work Regulations 1989.
Key Components of Factory Electrical Maintenance
1. Regular Inspections
Routine inspections are the first step to identifying potential issues.
Visual Checks: Identify exposed wiring, corrosion, or overheating components.
Thermal Imaging: Detect hotspots in circuits and equipment to prevent failures.
2. Testing and Monitoring
Comprehensive testing ensures systems remain functional and compliant:
Electrical Installation Condition Reports (EICR): A detailed assessment of a facility’s electrical infrastructure, recommended every 3-5 years.
Portable Appliance Testing (PAT): Annual checks for portable equipment like drills and power tools to ensure they meet safety standards.
3. Preventative Maintenance
This proactive approach minimises costly breakdowns:
Component Replacement: Replace ageing parts before they fail.
Panel Cleaning: Regularly clean and tighten electrical panels to prevent overheating.
Surge Protection Upgrades: Safeguard systems from voltage spikes.
4. Emergency Preparedness
Factories should have a robust contingency plan for power outages:
Backup Generators: Ensure critical machinery can function during outages.
Emergency Response Plans: Provide staff with clear procedures for handling electrical failures.
Unique Challenges in Factory Environments
Factories often have specialised equipment requiring unique maintenance strategies:
Transformers: Regularly inspect for insulation breakdown or overheating.
Motors: Maintain lubrication and clean motors to prevent energy inefficiencies.
Energy Audits: Identify opportunities to reduce energy consumption and operational costs.
For tailored electrical solutions, TLO Electrical Services offers expertise in managing these industrial complexities, ensuring compliance with British Standards (BS 7671) and maximising operational efficiency.
How TLO Electrical Services Supports Your Factory
TLO Electrical Services, based in Birmingham, provides a full suite of industrial electrical maintenance services, including:
EICR and PAT Testing: Ensuring compliance with UK regulations.
Preventative Maintenance Plans: Customised to the specific needs of your facility.
For more information, visit TLO Electrical Services.
TLO Electrical Services Ltd
Professional Electrical services for Health, Commercial, Industrial and Domestic installations.
Contact
Kingsbury Road, Curdworth, Warwickshire B76 0DE
3 Reindeer Park Lodge
© 2024. All rights reserved.
01827 52208
Privacy Policy